6-3 도요타의 사고방법
前項과 같이 과잉제조를 없애고 필요한 것을 필요할 때 하나씩 만들기 위해서는 「필요시」가 언제인가를 알아야 한다.
여기서 택트 사고방식이 중요하게 다루어진다.
택트타임이란 제품 하나를 몇분(초)로 만들면 좋을 지에 대한 시간이다.
이것이 반드시 제품의 필요수량부터 역으로 계산해야 한다.
간단하게 공식화하면 다음과 같다.
택트타임 = 1일 가동시간 / 1일 필요수(개)
그런데 때로 택트 구하는 방법을 틀리게 하는 라인을 볼 수 있다.
택트를 현재의 설비능력으로 공수에서 계산하고 있다.
즉 지금은 설비능력이 이것 뿐이어서 사람이 이것밖에 없으므로 이것은 한 개를 몇분,몇초로 해야 된다.
이것이 택트라 하는 것이다.
이 사고방식은 도요타식 생산시스템에서 완전히 틀린 것으로 주의하지 않으면 안된다.
설비능력은 어느 정도 고정되어버리지 만 사람을 증가하거나 줄이는데 따라 라인 능력이 증감한다.
정확한 의미인 택트부터 사람을 나눔에 따라 필요 최소한 사람으로 작업 할 수 있으므로 지금 있는 사람으로 할 수 있는 데까지 한다는 건 그의 능력과잉으로 재고가 쌓이고 만다.공수 절감으로 연결할 수 없다.
다음에 택트가 결정한 이것을 정확하게 지키게 하려면 어떻게 하면 좋을지 구체적으로 他節에서 논하고, 일반적으로 말하자면
(가)라인작업시・・・컴베아에 구역선을 그어 한 구역에서 하나제품을 그려 정확하게 지켜서 흘리게끔(페이스 메이커).
(나) 공정간・・・간판을 붙혀 간판이 제외되지 않으면 일을 해서는 안되는 룰로 한다.
간판에 대해서는 제4절에 설명되어 있어 참조하길 바란다.
공정간 간판의 큰 역할은 과잉제조를 억제하고 적절한 택트(필요시)가 전공정에서 알게끔 할 수 있다는 것을 충분히 이해할 수밖에 없다.
6-4 작업 재배분
이상을 실시함에 따라 과잉제조가 생기지 않으며 작업자 무다는 작업대기、기타로 표면화 된다.
다음은 제1항(현장작업 중 사실 인식)에서 부가가치가 없는 작업(부수작업)과 관련 해 그다지 비용을 들이지 않고 전공정에도 그다지 영향주지 않는 것에 대해서 개선한다.
예를 들면 부품을 가지러 가는 경우는 부품선반을 이동하여 걷는 시간을 없앤다.이렇게 라인을 정리한 후 각자 작업 재분배를 진행한다.
배분은 택트 중에는 정미작업과 현재 아무리 해도 생략할 수 없는 작업만 준다.
그것을 간단히 그림에서 설명하면 다음과 같다.
그림5
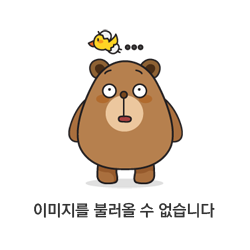
이 경우 특히 주의할 것은 아래 그림과 같이 「작업자Ⅳ의 여력을 4인으로평균 할당해서는 안된다.」라는 것이다.
그림 6
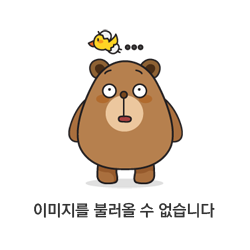
그 이유는 애써 낭비를 명확히 하여 문제의 소재가 누구라도 알게끔 개선의 필요성을 발생시키지만 평균화로 되어버림에 따라 숨어 버리기 때문이다.
더욱이 전원이 0.15씩 여유(=작업대기)를 가지고 일을 계속한다면 ,만약 그것이 10일간 계속되면 작업 베이스로 고착되버린다.
그로 인해 다음 개선에 대하여 일의 량이 증가하여 고되다는 심리적인 저항이 되는 경우가 많기 때문이다.
5그림 예에서 5인서 하는 일을 낭비를 제거하여 순서로 한 결과、계산상은 3.4인이 완성할 수 있게 된다.그러나 0.4인이란 없기에 이것도 1인이다.
즉 1인을 줄일 수 있으며 이미 1인은 40%만의 일이 있는 상태이다.
이상과 같이 일의 재배치에 따라 1인을 줄였다.(작업자Ⅴ을 줄인다.)
다음으로 중요한건 작업자Ⅳ의 여유작업이다.
결론부터 말하면 0.4인공의 작업을 제거하여 개선하는 것이 다음 목표가 된다.
이 0.4인공을 일손을 빌리지 않고 한다면 어떨까
초점을 그것에 맞춰 여러가지 안을 생각할 수 있다.
안 중에는 설비를 자동화하는 비용이 드는 안도 있거니와 자그마한 슈트를 만들어 걷는 시간을 단축하거나 빠레트를 작게 하여 손이 미치는 곳에 배치하는 그다지 비용이 들지 않는 안도 있다.
이 단계에서 과대한 안을 택하지 않는 것이 중요하다.
목적은 0.4인분의 작업을 제거하기 때문이다.
이것에 어울리는 제일 저렴하고 실행하기 쉬운 안을 채택한다.
그리하여 5인서 해온 작업을 비교적 작은 금액으로 2인을 줄일 수 있다.
다음에 다시 한번 라인을 재점검 해본다 .
자세히 보면 빠뜨린 낭비를 발견하게 될 것이다.
때로는 부가가치가 없는 작업 할당에 알맞은 작업으로서 지금은 방법없이 시키지만 돈이 되지 않기에 어떻게 든 그만두게 할까 라고 생각하는 것이 중요하다
이러한 것을 모아 개선한다면 이제 1인을 줄일 수 없는지에 대한 과제로 도전해 볼 수 있다.
이번은 전처럼 간단히 할 수 없는 것이 당연히 많을 것이다.
어느 안을 택해도 돈이 대량 들거나 전후공정에 상당히 영향을 주고 만다.
때에 맞춰 지금 당장 실현할 수 없을지도 모른다.
그러나 단념하지 말고 항상 문제 의식을 가지고 매일 현장을 보면 무엇인가 힌트를 얻고 멋있는 안을 생각해 낼 수도 있다.
또한 판매진행에 따라 택트가 바꿔거나 모델교체로 설변이 되든가 하는 새로운 수요가 발생할 시 꼭 되살릴 수 있는 실현이 가능하게 된다.
따라 현재 당장 할 수 없는 것도 단념하지 말고 진정으로 일에 몰두하는 것이 중요하다.
'생산 > 도요타 생산방식' 카테고리의 다른 글
도요타 생산방식 소개16(개선과 감독자) (0) | 2022.11.02 |
---|---|
도요타 생산방식 소개15(개선의 순서) (0) | 2022.11.02 |
도요타 생산방식 소개13(공수절감1) (2) | 2022.10.27 |
도요타 생산방식 소개12(안전) (0) | 2022.10.26 |
도요타 생산방식 소개11(안전) (0) | 2022.10.26 |