각 용접법의 특징 및 종류
용접법은 열원에 따라서 다음과 같이 분류할 수 있다. 이중에서 일반적으로 널리 쓰이는 것은 Oxy-acetylene Gas Welding법과 Gas Tungsten Arc Welding 등이 있다. Electro-slag Welding의 경우에는 아크 용접법이 아니지만 처음의 시작단계에서 아크를 사용하므로 아크용접법 또는 세미-아크용접법으로 분류하기도 한다.
표 1. 열원에 따른 대표적인 용접법
열 원 | 용 접 법 | 약 칭 |
Gas | Oxy-acetylene Gas Welding | OAW |
Arc | Shielded Metal Arc Welding | SMAW |
Gas Tungsten Arc Welding | GTAW | |
Plasma Arc Welding | PAW | |
Gas Metal Arc Welding | GMAW | |
Submerged Arc Welding | SAW | |
Arc (Semi-Arc) | Electro-slag Welding | ESW |
High Energy | Electron Beam Welding | |
Laser Beam Welding |
다음의 그림 1에는 가스용접(Gas Welding), 아크용접(Arc Welding) 및 전자빔 용접법(Electron Beam Welding)법을 도시하였다. 그림에서 보는 바와 같이 다른 방법에 비하여 일렉트론빔 용접의 폭이 제일 좁으며 에너지의 효율이나 속도가 좋다.
그림 1. 가스, 아크 및 고에너지빔 용접법의 비교
● 아크 용접 전기회로에 2개의 금속 또는 탄소단자를 서로 접촉시키고 이것을 당겨 간격이 생기게 하면 아크를 발생하면서 고열이 생긴다. 이 열을 이용한 용접이 아크 용접 법이다. 이 때 고열로 인하여 단자의 일부가 기화되고 전기 통로가 되어 전류는 계속 흐르게 된다. 이 때 발생하는 열로써 금속을 용융시킬 수 있다. 가장 온도가 높은 부분은 탄소 아크에서 4000℃ 금속 아크에서는 3000℃에 달한다. 그림 2. 시일드 메탈 아크용접법의 개략도 그림 3. 가스-텅스텐 아크 용접의 개략도 모재와 금속전극과의 사이에 아크를 발생시켜 그 용접 열로서 전극과 모재를 용융하며 용접 금속을 형성하는 것을 금속 아크 용접의 방법 , 이 방식의 용접을 용극식 용접법이라고 한다. 피복 아크 용접법 , 서브머어지드 아크 용접법 , 불활성 가스 금속 아크 용접법 , 탄산가스 시일드 아크 용접법 등이 이에 속한다. 탄소 아크에 의하여 용접 열을 공급하고 용착 금속은 별도로 용가재를 사용하여 이것을 녹여 공급하는 것을 탄소 아크 용접 방법이라 하고 이 방식의 용접을 비용극식 용접법이라고 하며 오늘날의 불활성 가스 텅스텐 아크 용접법은 이 방법이 발전된 것이다. 아크 용접법의 초기에는 직류 전원을 사용하였다. 그러나 피복용접봉의 발명으로 그 후 교류 전원에 의한 용접법도가능 가능하게 되었다. 교류아아크 용접기는 효율이 좋고 가격도 싸며 보수와 취급등이 쉬우므로 널리 사용되고 있다. 금속 용접봉에는 심봉의 주위에 특수 용재의 피복을 한 피복 용접봉이 사용되고 용접할 때 피목제가 고온에서 가스를 발생시키든가 또는 슬랙이 되어 공기중의 산소와의 화학 작용을 방지하여 용융 금속을 보호함으로써 좋은 용접이 되도록 한다. 보통 공기 저항을 깨트리고 아크를 발생할 수 있는 개로 전압은 직류에서는 50-80V 교류에서는 70-135V 이다. 아크 발생 후에는 전압이 감소되므로 아크를 계속하는데 필요한 아크 전압은 20-30V 이다. 그러나 피복 용접봉을 사용하면 다소 차가 있으며 발생된 아크는 안정한 상태를 유지하도록 작업 조건을 조절해야 한다. 직류를 사용한 아크는 전체 발열량의 60-75% 가 양극 측에 발생한다. 교류를 사용하면 교번 전류로 인하여 양극의 발열량이 동일하게 된다. |
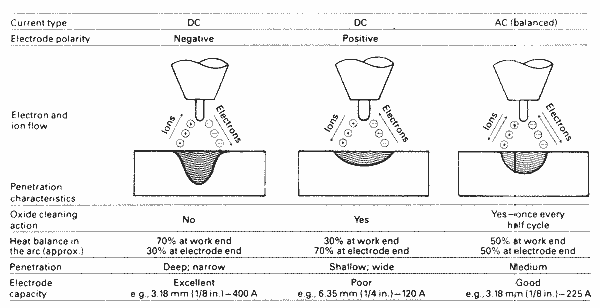
● 아크 용접기 크게 직류와 교류 용접기로 나눈다. 직류 용접기는 동력선의 전력을 을 사용하여 전동기를 회전하고 이것에 직결된 직류 발전기를 직결하여 운전함으로써 용접 직류 전원을 얻는다. 교류 용접기는 일종의 변압기로서 2차 측 코일에서 용접 전류를 얻는다. 아크 전압은 개로 전압에 비하여 낮으므로 작업할 때에 손실이 많아 불리하다. 용접기는 아크의 발생이 쉽고 작업할 때에 능률이 좋도록 설계되어 있다. 그림 4. 가스-텅스텐 아크 용접법의 개략도 그림 5. 세가지 전류형태에서의 가스-텅스텐 아크용접법 그림 4에는 대표적인 형태로서 가스-텅스텐 아크용접법을 나타내었다. 5에는 3가지 다른 전류 형태에서의 아크용접법의 개략도를 나타내었다. |
◆ 직류 아아크 용접기 (1) 정전압형 직류 용접기 : 부하가 변동하여도 전압이 일정하게 되어 있다 발전기의 용량이 충분하면 많은 용접을 동시에 할 수 있다. 한대의 발전기로서 여러 개의 회로를 끄집어 내어 각기 용접공은 직렬저항과 리액턴스를 연결하여 아크 전류를 통하게 한다. (2) 정전류형 직류 용접기 : 전류가 항상 일정하다. 아크 전압이 자주 변하여도 아크 전류는 일정하여 아크가 안정되어 있다. 이 방식에는 단식 직류 발전기 즉 한대의 발전기에서 한사람의 용접공이 용접 전류를 공급받을 때 편리하며 기계 설비가 적고 아크 발생이 쉬운 장점이 있다. |
◆ 정전력형 직류 용접기 전류가 증가하였을 때 자동적으로 전압이 강하 되도록 설계된 것이므로 대략 일정한 전력을 갖게 된다. 단식과 복식의 용접기가 있다. |
◆ 직류 용접기의 특징 전류가 한 방향으로 흐르기 때문에 아크가 안정되어 피복없는 용접봉으로도 용접할 수 있다. 그러나 아크의 길이가 너무 길어 용입 불량이 되기 쉽다. '+' 를 모재로 하고 용접봉을 '-' 로 연결한 경우를 정극성 이라 하고 그 역을 역극성이라고 한다. 직류 용접기에는 마그넷 불로우 현상이라고 하여 아크가 일정 방향으로 흐르는 일이 있다. 이것을 직류에서 용접봉 또는 모재의 주위에 자력선이 생기고 그 분포에 와류가 생기기 때문이다. 이것은 불량 용접의 원인이 되므로 이것을 방지하기 위해 모재의 케이블 연결점을 바꾸던가 가접부를 크게 하고 후퇴 용접하여 방지하나 방지 곤란한 것도 있다. |
◆ 교류 아크 용접기 보통 교류 아크 용접기는 일종의 변압기 이나 2차 전류를 통과시킬 때 즉 용접할 때 계단적으로 2차 전압이 떨어지는 특성을 갖도록 설계되어 있다. 그러므로 일반 교류 아크 용접기는 아크를 안정시키기 위하여 회로에 리액턴스 코일을 넣어 리액턴스를 크게 함으로써 아크 부분의 저항 변화로 생기는 2차 전류의 변화를 적게 하고 있다. 리액턴스를 크게 하고 개로 전압을 높게 함으로써 용접기의 효율이 25-40% 정도로 된다. 교류 용접기는 직류 용접기에 비하여 안정성이 떨어지나 가격은 1/3~1/4 정도 이므로 직류 용접기보다 널리 사용되고 있다. |
◆ 고주파 아크 용접기 교류 아크 용접기에 사용되는 변압기 중에는 고주파 발생장치를 장비하고 있는 것이 있어서 용접 전류를 5-200000 사이클의 고주파 전류로 변화시킨다. 그 회로는 용접할 때 전류를 안정하게 하고 10-50A 의 적은 범위의 아크 전류에서도 쉽게 작업할 수 있다. 보통 용접기로서는 용접이 곤란한 비교적 엷은 판재의 용접도 가능하고 또한 Cu , Al 등도 효과적으로 용접할 수 있다. |
◆ 자동 아크 용접기 용접봉을 기계 장치로써 피이드하고 아크의 길이를 일정하게 하는 동시에 안정한 작업을 하기 위하여 자동 용접기를 사용한 용접법이 있다 (1) 반자동 용접법 (2) 자동 용접법 일반으로 반자동 용접법은 용접의 피이드를 손으로 하여준다. 자동 용접법의 장점은 다음과 같다. (1) 용접 속도가 수동식에 비하여 빠르며 3-6 배에 달한다. (2) 아크가 안정되어 우수한 용접이 가능하다. (3) 작업자에 관계없이 능률적으로 작업할 수 있다. (4) 대량 생산으로 생산비가 싸게 든다. 자동 용접기는 용접열을 용접기에 부속되어 있는 로울러에서 용접부에 공급하면서 연속적인 용접을 하는 방법이다. 용접봉은 이송용 전동기로써 회전하는 로울러 사이에 끼어 있어 로울러의 회전은 아크의 길이 즉 아크 전압의 변화에 따라 이송용 전동기의 속도가 변하도록 되어 있다. |
◆ 직류 용접기와 교류 용접기 비교 - 직류 (1) 아크가 교류보다 안정되나 마그넷 불로우가 있다. (2) 무부하 전압이 교류보다 작고 전격의 위험이 교류보다 작다. (3) 발전형 직류 용접기는 소음이 있고 회전부 고장이 많다. 정류기의 손상 및 고장에 주의해야 한다. (4) 교류에 비해 가격이 비싸고 유지 보수 점검에 교류보다 시간이 더 걸린다. - 교류 (1) 전류 전압이 교번하므로 아크가 불안정하다. (2) 취급이 쉽고 고장이 적다. (3) 값이 싸다. (4) 무부하 전압이 직류보다 크고 전격의 위험이 크다. |
◆ 아크 용접봉 초기에는 금속봉을 그대로 사용하였으나 이것은 다음과 같은 결점이 있다. (1) 보존 중에 대기 중의 습기와 산소의 영향으로 녹이 생겨 용착이 잘 된지 않는다. (2) 용접할 때 고온 기화로 용접 부분의 재질이 불량하게 되기 쉽다. (3) 용접부가 공기와 접촉하여 산화물이 생긴 것이 용접 부분에 들어가기 쉽다. 그래서 최근에는 특수한 때 이외에는 전부 용접봉의 주위를 피복한 피복 용접봉이 사용된다. 피복 용접봉은 피복제의 종류에 따라 여러가지 형이 있다. 보통 사용되는 심선의 직경에는 0.1 , 1.4 , 2.0 , 2.6 , 3.2 , 4.0 , 5.0 , 6.0 , 7.0 , 8.0mm 등 10종이 있으나 그중 3.2-6mm 가 널리 사용되고 특히 4mm 가 가장 많다. 심선의 재질은 주철 특수강 비철 합금에는 모재 성분과 동일한 것이 널리 사용된다. 연강에는 탄소가 비교적 적은 연강봉이 사용된다. C가 비교적 적은 것을 사용하는 이유는 강철의 연성을 크게 하고 용해 온도를 높게 함으로써 잘 용해되도록 하여 용접 조작을 쉽게 하기 위한 것이다. Mn 은 탈산제의 역할을 하고 S의 유해 작용을 감소시킨다. 또한 너무 많으면 취성이 있고 용접이 곤란하므로 일정한 범위로 한다. P는 상온 취성이 있어서 용접부에 균열이 생기는 원인이 되기 쉬우며 S는 고온 취성이 있어서 S와P는 될수록 적게 한다. |
◆ 피복제의 첨가물 (1) 가스 발생식 용접봉 : 고온에서 가스를 발생하는 물질을 피복제 중에 첨가하여 용접할 때 발생하는 활원성 가스 또는 불활성 가스 등으로 용접 부분을 덮어 용융 금속의 변질을 방지하는 용접봉이다. 유기물형 용접봉이라고도 한다. 슬랙은 쉽게 제거되고 다공성이 있어서 잘 부서지며 산성이다. 아크는 대단해 안정되고 불활성 가스에 둘러싸여 용접 속도도 크게 할 수 있다. (2) 슬랙 생성식 용접봉 : 피복제에 슬핵화하는 물질을 주성분으로 사용하여 용융 금속의 입자가 용접봉으로부터 모재에 이동되는 사이에 슬랙을 형성하여 내부를 보호하며 대기와의 화학 반응을 저지하여 용착 금속을 정련하고 또한 냉각과 더불어 응고되어 용착 금속의 표면을 덮어 급랭 산화 및 질화 등을 방지하는 역할을 하는 용접봉이다. 피복제는 무기물로 되어 있으며 이 형식의 용접봉을 무기물형 용접봉이라고도 한다. (3) 반 가스식 용접봉 : 앞의 두 가지의 특징을 결합한 용접봉이다. 용융 금속을 보호, 아크를 안정, 용융 금속을 정련, 용착 금속의 급랭을 방지, 용착 금속에 필요할 원소를 보충 등의 여러 조건을 구비하기 위해 여러 성분을 첨가하고 배합한다. 피복제의 성분으로 산화물계에는 SiO2 , CaO , Al2O3 , MnO2 등이 사용되고 규산염계에는 Na2Si4O7 , Na2SiO2 등 탄산염 계에는 CaCO3 , Na2CO3 , MnCO3 , NaHCO3 등과 불화물 유기물 붕산염 으로는 Na2B4O7 + 10H2O 또는 Na2B4O7 + 5H2O 가 사용되며 철합금 계로는 FeSi , FeMn 등이 사용된다. 이 중에서 몇 개를 잘 혼합하고 물을 첨가하여 혼합한 후 그대로 도포제로써 사용하든가 또는 수분을 줄이고 기계적으로 압착하여 피복제로써 사용한다. 고착제로서 수성 유리 , 아교 , 젤라틴 , 아라비아 고무 , 해초 등이 사용되고 그 밖의 섬유 물질로서 석면을 혼합하는 일도 있다. |
◆ 아크 용접부의 기본 현상 아크 발생에는 탄소 또는 금속봉을 전극으로 사용한다. 중심의 백열부분은 아크 중심이다. 중심 주위의 청색 부분을 아크 유동부라고 한다. 중심 주위의 황색을 띄고 있는 부분을 아크 플레임이라 한다. 용접부의 조직 : 용접 부분의 특성은 모재와 동일한 것인 동시에 균일한 재질이 요구된다. 또한 전체적으로 물리적 성질 및 응력 분포도 동일한 것이 필요하게 된다. 그런데 아크 용접 과정을 볼 때 아크열로서 용접봉은 용해 과열 산화 기화 등의 작용을 받게 된다. 이때 공기중의 O2 및 N2 등과 반응을 일으켜 산화물 및 질화물을 형성하여 용접 결함을 초래한다. 이것을 피복 용접봉에 도포된 용제의 화학적 반응으로 방지하고 있다. 용접부에서 거리가 멀어 용접의 영향을 받지 않는 원질부 , 용접부와 인접되어 있어 입상의 큰 조직으로 변질되는 변질부 , 모재와 용접봉이 융합된 부분이므로 각 부분의 조직 및 결정의 변화가 생기는 융합부로 용접 부분이 이루어져 있다. 용착 금속 부분은 용접봉이 용접되어 형성된 것이다. 각 조직의 변화는 뚜렷한 경계선을 얻기 곤란하다. 탄소는 저온에서 고온으로 확산되는 경향이 있으므로 융합부에는 탄소량이 많아지고 모재에 인접된 부분은 모재보다 탄소량이 적어진다. 따라서 융합부는 급랭에 의한 영향을 받기 쉽다. 과열부 중에서 융합부에 가까운 부분은 용융할 때의 고온의 영향을 받아 페라이트는 오스테나이트의 경계에 석출된다. 일반적으로 강철을 용접하면 용융 열로써 강철은 경화되고 또한 여리게 된다. 그러므로 용접 부분은 충격과 피로에 약한 결점이 있다. |
◆ 용착 아크 용접의 모재와 용접봉을 용융시켜 일체로 만드는 것을 용착이라고 한다. 용착은 용접부의 양부 및 강도를 검사할 때 중요한 인자가 되며 용접봉의 적당과 부적당 및 용접 온도 아크의 길이 전류량 용접 속도 등과 밀접한 관계가 있다. 용착 깊이는 크레이터의 깊이에 따라 알 수 있다. 크레이터 부분에서는 모재와 용접봉이 융합되며 크레이터 부분은 용접의 진행과 더불어 이동된다. 보통 크레이터의 깊이는 용접 재료의 두께에 따라 다르나 적어도 1.6mm 이상은 되어야 한다. 용점은 급한 용융 상태이므로 모재면의 융해된 부분에 용융 금속이 꽉 차 있지 않으면 모재와 용착 금속의 경계에 오목한 부분이 생겨 언더컷 현상을 일으킨다. 또한 모재와 충분히 융합되지 않은 상태로 모재면에 닿아 있으면 오버랩이 생긴다. 언더켓은 용접 속도가 빠르고 전류가 많을 때에 일어나며 오버랩은 용접 속도가 느리고 용접봉이 과융해되고 전류가 많을 때 일어난다. 강의 용접성은 용접이 한 덩어리로 잘되는 것을 의미하므로 용접성이 좋고 나쁨은 용접경과의 결합상태 또는 난이도로 표시할 수 있다. |
◆ 아크의 크기 아크가 너무 길 때에는 (1) 아크가 불안정하다. (2) 용착이 얇게 된다. (3) 용접부의 금속 조직이 취약하게 되어 강도가 감소된다. (4) 아크 열의 손실이 생긴다. (5) 용접봉이 불경제가 된다. 아크가 너무 짧게 되면 아크를 지속하기 곤란하고 용접을 연속적으로 하기 곤란하며 용착이 불량하게 된다. 금속 용접봉을 사용하여 좋은 용접조건을 얻기 위하여 아크의 길이는 짧은 것이 최대 필요 조건이다. 짧은 아크는 긴 것보다 안전성이 있고 작업이 용이하다. |
◆ 아크 용접 시공 (1) 용접의 방향과 자세 특수 용접으로서 연질 모재의 표면에 경질 용접봉으로 용접하여 경질 표면층을 형성하는 하드 페이싱 방식도 있다. 또는 마모된 부분품의 표면에 같은 재질의 용접을 하여 본래 치수로 만드는 덧살 용접에 대하여 현장에서는 흔히 빌트업 용접이라고 부른다. 이중 가장 많이 쓰이는 이음법은 맞대기 용접이다. 작업자의 운봉은 자세에 따라 다음과 같은 종류로 분류한다. (2) 용접작업 용접할 재료를 소정의 치수로 절단하고 끝도 지정된 치수로 가공한다. 용접자세는 아래보기가 좋으며 필요하면 지그를 사용하여 작업을 용이하게 하고 동시에 변형 방지 공정수의 절약 정밀도를 높이고 다량 생산을 할 수 있도록 연구한다. 용접부에 녹이 있으면 이것을 제거하고 습기도 없게 한 후에 작업을 한다. 여러 층으로 용접할 때에는 각 층마다 슬랙을 완전히 제거한 다음에 다음 층의 용접을 한다. 모재 전체를 용접하기 전에 재료를 정확히 맞추고 가용접을 한다. 가용접은 용접선을 따라 군데군데 용접하는 것을 말하며 변형을 방지하기 위하여 보조재를 덧붙여 가용접할 때도 있다. 고탄소강 , 주철 , 특수강 등은 용접할 때 터지기 쉬우므로 재료를 용접하기 전에 모재를 100-400℃정도로 가열한다. 가열에는 목탄 , 산소-아세틸렌가스 , 괴탄 등을 사용한다. 용접의 순서는 변형 잔류 응력의 방지 , 공정수의 절약을 고려하며 모재의 재질 판의 두께 형상 용접 자세에 따라 적당한 용접봉의 종류 크기 용접 조건을 선택한다. 아크를 발생시키기 위해서는 용접봉으로 모재를 가볍게 두드리면서 뗀다 떼는 거리는 보통 3-5mm가 적당하다. 아크가 용접 중에 중단되면 크레이터가 나타나며 다시 아크를 발생시킬 때에는 크레이터 조금 전방에서 발생시키고 크레이터의 후단으로 가져가서 용접을 시작한다. (3) 비이딩 또는 운봉법 용접봉을 움직이는 방법은 용접선 위를 직선으로 움직이는 것과 용접선에 직각 방향으로 움직이며 진행하는 위이빙 방법이 있다. 전자에서는 직선 비이드가 나타나며 후자에서는 폭이 넓은 비이드를 얻을 수 있다. 위이빙은 각 층마다 용착되는 금속의 양을 증가할 목적으로 하며 안정된 아크로 진행하여야 된다. 이와 같은 비이딩의 요령은 결코 고정된 것이 아니고 작업자에 따라서 여러 가지로 다른 운봉법을 채택하고 있다. 비이드의 중앙은 양끝보다 높은 온도가 되므로 끝에서는 운봉 속도를 느리게 한다. 비이드는 여러 틈으로 겹치는 것이 변형을 방지하는데 유리하다. 판의 두께가 두꺼울수록 층의 수를 증가시킨다. 비이드는 한 끝에서 연속적으로 다른 끝으로 진행하는 점진식 외에 여러 가지방법이 있다. (4) 용접봉의 각도 현재 피복된 용접봉에 대하여서는 60-80°로 하는 것이 적당한 것으로 되어 있으나 작업 조건의 영향이 크다 용접 전류는 판 두께, 이음 모양, 용접 자세, 봉의 종류, 봉 지름, 층수에 따라 다르다. 전류가 강하면 스패터링이 많고 용융 속도가 빨라지며 언더컷이 일어나기 쉽다. 전류가 약해지면 용융이 늦고 녹은 덩어리의 스패터가 커지면서 모재에 옮겨지는 까닭에 용입 불량과 오버랩이 생긴다. 전류의 조정은 실제 작업에서는 항상 주의하여야 한다. (5) 용접 입열 용접부에 외부에서 주어지는 열량을 용접 입열이라 한다. 피복 용접봉을 사용한 경우 길이 1cm 당의 아크 용접에서 발생하는 전기적 에너지 H, 아크 전압 E(V), 아크 전류 I(A), 용접 속도 v(cm/min)일 때 H = 60 E I / v (joule/cm) 실제는 이 전기적 에너지 이외에 피복제의 분해에 따른 화학적 열에너지가 위의 H에 가산되어야 한다. 실제 소비되는 용접 입열은 용접봉의 용융열이 약 15% 용접금속의 형성열이 20-40% 이고 모재의 가열 피복제의 용해 복사 및 대류 등에 대한 열 60-85% 이다. |
● 전기 저항 용접 용접할 물제에 전류를 통하여 접촉부에 발생되는 전기 저항열로서 모재를 용융 상태로 만들고 외력을 가하여 접합하는 용접이 전기 저항 용접법이다. 이 때에 발생하는 저항열은 줄의 법칙에 따르며 다음 식으로 표시된다. Q=0.24I*IRt 여기서 Q:열량(cal) , I:전류(A) , R:전기저항(Ω) , t:시간(sec) 이다. 그러므로 저항이 큰 재료에 저전압인 전원에서 많은 전류를 통과시켜 이 때 발생하는 저항열을 이용한다. 전기 저항용접의 종류에는 다음과 같은 4종류가 있다. (1) 맞대기 용접은 모재의 단면을 맞대어 놓고 맞대임 접합하는 방식이다. (2) 스포트 용접은 2장 또는 3장 이상의 금속판을 겹쳐 놓고 리벳 접합하듯이 점상으로 용접하는 방식이다. (3) 시임 용접은 연속적으로 스포트 용접을 하는 방식이다. (4) 프로젝션 용접은 돌기의 접촉부를 용접하는 방식이다. 전기 저항 용접은 아크 용접에 비하여 많은 전류를 단시간에 흐르게 하는 것이 필요하다. 또한 정밀한 제어장치가 요구되며 용접 온도는 아크 온도보다 저온이고 작업속도가 빠르고 용접 부분의 안정성이 크다. 전기 저항 용접의 열원은 저항 발열과 방산열의 차이로써 얻어지므로 열전도율이 좋은 모재는 열이 전달되기 쉽고 또한 접촉부가 냉각되어 많은 전류를 짧은 시간내에 흐르게 하여야 한다. 일반적으로 고유 전기 저항이 크고 열전도율이 작으며 용융점은 낮고 또한 소성 구역 온도 범위가 넓은 금속일수록 저항 용접이 쉽다. 조작은 거의 기계적이고 다른 용접법처럼 사람의 기능의 우열에 영향이 적고 또한 용접에 필요한 시간도 적으므로 대량 생산에 적당하다. 현재 전기 저항 용접법은 금속 아크 용접법에 이어 광범위하게 쓰여지며 자동차 비행기 공업은 물론 제관 공업 기타 방면에도 이용되고 있다. |
◆ 맞대기 용접법 금속선 , 봉 , 판 등의 끝면을 맞대어 용접하는 것 (1) 업셋 버트 용접 : 단순히 맞대기 용접이라고도 한다. 전류를 통하기 전에 용접재를 압력으로써 서로 접촉시키고 이것에 대전류를 흐르게 하여 접촉 부분이 전기 저항열로써 가열되어 용접 온도에 달하였을 때 다시 가압하여 융합시키는 방법이다. 이때 용접 부분은 고온으로 되고 열소성 상태로 되어 있으므로 가압하면 접촉부는 블록형으로 부풀어 모재의 길이가 다소 짧게 된다. 피용접재를 세게 맞대고 여기에 대전류를 통하여 이음부 부근에서 발생하는 저항 발열에 의해 가열시켜 적당한 온도에 도달하였을 때 축 방향을 센 압력을 주어 용접하는 방법이다. 압력은 수동식으로 가하는데 이때는 스프링 가압식이 많이 쓰이고 있다. 대형 기계에서는 공기압 , 유압 , 수압 등이 사용되고 있다. 전극은 전기 전도도가 좋은 순 구리 또는 구리 합금의 주물로서 만들어지고 있다. 변압기는 보통 1차 권선 수를 변화시켜 2차 전류를 조정한다. 이것은 2차 권선 수가 대부분 단권이기 때문이다. 이 밖에 전류 조정기 , 전원 개폐기 , 자동 전류 차단기가 있다. 맞대기 용접법에서는 가스 압접법과 같이 이음부에 개재하는 산화물 등이 용접 후에도 남아 있기 쉽고 용접하기 전의 이음면의 끝맺음 가공이 특히 중요하다. 맞대기 용접법은 플래시 버트 용접법에 비하야 가열 속도가 늦고 용접 시간이 길다. (2) 플래시 버트 용접법 : 용접할 재료를 서로 접촉시키기 전에 적당한 거리에 놓고 서로 서서히 접근 시키면서 대전류를 통전시킨다. 용접 재료가 서로 접촉하면 돌출된 부분에서 전기 회로가 생겨 이 부분에 전류가 집중되어 스파크가 발생되어 접촉부가 백열 상태로 된다. 용접물이 더욱 접근됨에 따라 다른 접촉부가 같은 방식으로 스파크가 생겨 모재가 가열됨으로써 용융 상태가 된다. 작당한 고온에 달하였을 때 강한 압력을 가하여 압접한다. 특징으로는 (1) 가열 범위가 좁고 열 영향부가 작다. (2) 용접면에 산화물이 생기지 않는다. (3) 신뢰도가 좋고 이음 강도가 크다. (4) 동일한 전기 용량에 큰 물건의 용접이 가능하다. (5) 용접 시간이 짧고 소비 전력이 적다. (6) 종류가 다른 재료의 용접이 가능하다. |
◆ 맞대기 용접 조건과 용도 업셋 용접법은 강철선 구리서 알루미늄선 등의 인발 작업에서 선재의 접합에 사용되는 일이 많고 또한 연강의 각종 단면 , 둥근 봉재 , 단면재 , 파이프 등의 접합에 사용한다. 플래시 보트 용접은 레일 , 보일러 , 파이프 , 드릴 몸체의 용접 , 건축재료 , 자전거의 림 , 파이프 각종 봉재 등 중요한 부분의 용접에 사용된다. |
◆ 스포트 용접 점 용접이라고도 하며 주로 판재의 용접에 사용된다. 리벳 이음은 판재에 구멍을 뚫고 리벳으로 접합시키나 스포트 용접은 구멍을 뚫지 않고 접합할 수 있는 장점이 있다. 이 방법은 전극 사이에 용접물을 넣고 가압하면서 전류를 통하여 그 접촉 부분의 저항열로 가압 부분을 융합시킨다. 이 융합 부분을 너겟 이라고 한다. 스포트 용접을 잘 하려면 가압력 , 통전시간 , 전류밀도 등을 잘 조절하는 것이 필요하다. |
◆ 스포트 용접기의 구조와 이용 고정식과 이동식이 있는데 고정식은 프레스형 스포트 용접기 , 로코형 스포트 용접기 의 2종류가 있다. (1) 프레스형 스포트 용접기 : 가압용 실린더가 위에 있어 전극을 가압하는 기능을 갖고 있으며 보통 압축 공기를 사용한다. 몸체로부터 상하 2개의 아암이 있고 그 선단에 전극 고정 장치가 있다. 상하 2개의 아암의 길이와이동거리는 가공할 수 있는 용접물의 크기와 관계가 있다. 보통 이것으로 용접의 능력을 표시한다. (2) 로커형 스포트 용접기 : 상부 아암의 레버 장치로서 가압 작용을 하게 되어 있다. 가동구가 비교적 중량이가볍고 상부 전극이 쉽게 이동할 수 있게 되어 있다. (3) 고정식 스포트 용접기 : 용접할 물건을 이동하게 되므로 너무 큰 형상을 하였던가 또는 중량이 너무 무거운 것은 스포트 용접을 하지 않는다. (4) 이동식 스포트 용접기 : 용접 변압기와 가압부로 나누어져 있고 케이블로 연결되어 있다. 보통 2.0nm이하의 엷은 판재 용접에 사용되고 용접 전류는 10000-15000A 전압은 2-10V 정도이다. 용접할 판재는 표면을 깨끗이 하고 산화 피막 및 유지류를 제거하며 강철판은 묽은 활산으로 씻고 샌드 블래스팅으로 흑피를 제거한다. 경합금은 산 알칼리 등으로서 화학적으로 깨끗하게 하든가 또는 기계적으로 산화막을 제거한 후 부착되어 있는 유지류는 잘 제거하고 작업한다. 강철에서는 두께의 차가 8배 이하 경합금에는 5배 이하로 한다. 스포트 용접부 표면을 깨끗이 하는 방법으로 산세 , 샌드 블래스팅 , 쇠솔로 떨기 , 아브레시이브 페이퍼 , 사염화탄소에 의한 그리이스 제거 등을 채택한다. 스포트 용접의 통전 시간과 소요 전력 : 스포트 용접을 하기 위하여서는 가압력 통전시간 전류의 크기에 주의하여야 한다. 가압력이 크면 접촉 저항이 감소하여 용접 경과가 좋지 않고 작으면 전류를 통과시킬 때 스파크가 나타나서 용접 경과도 좋지 않으며 전극과 용접 표면을 침해한다. 용접 표면은 깨끗이 하고 평탄하여야 되며 용제는 사용하지 않는다. 용접 재료가 구리 , 황동 , 알루미늄 일 때에는 소요 전력은 이 그림의 값의 약 5배나 필요하다. 용접 시간은 맞대기 용접에 비하여 가열 면적이 좁으므로 대단히 짧다 용접 온도에 도달하여 가압할 때 압력이 세면 용접부가 오목하게 들어가서 약해지며 압력이 약하면 완전한 용접이 안 된다. |
◆ 시임 용접법 시임 용접은 스포트 용접을 연속적으로 하는 것이라 생각할 수 있다. 스포트용접의 전극 대신 회전 로울러 형상을 한 전극을 사용하여 용접 전류를 공급하면서 전극을 회전시켜 용접하는 방법이다. 주로 공기의 밀폐성을 필요로 하는 용기, 긴 파이프 등 연속적인 작업에 쓰인다. 시임 용접용 로울러가 회전할 때 공급 전류의 일부는 먼저 용접된 부분에 흐르고 일부는 로울러 전극 사이에 흐르므로 공급 전류가 큰 것이 필요하다. 그러나 연속적으로 많은 전류가 통하면 용접 판재에 너무 많은 열이 생겨 용접부 전체가 용융되므로 통전을 단속적으로하여 냉각시간을 주는 방식이 사용되고 있다. 때로는 엷은 판재에 연속적을 전류를 통하여도 좋은 결과를 줄 때가 있다. (1) 시임 용접 조건 : 용접 전류는 스포트 용접 전류의 1.5-2.0배 가압력은 1.2-1.6배로하고 1mm의 연강판에는전류 15000A와 가압력 400kg 통전시간 및 정지 시간은 각각 1/20 초 정도이다. 전극은 동제 원판상으로서보통 250mm 전후의 것이 사용되며 그 밖에 둥근 것 평평한 것 등도 있다. 연속하여 많은 전류를 공급하면용접판에 주는 열량이 많아져서 용접부 전체가 용융 상태에 이르러 용접부 표면이 로울러에 의하여 흠 모양으로떨어져 나가기 쉽다. 이 결함을 방지하기 위하여 용접할 때 전류를 차단하여 전극을 가압한 대로 정지시키고용접부가 냉각한 후에 전류를 차단한 채고 로울러 전극을 다음 용접 위치까지 전진시키고 그 위치에서 앞에서설명한 공정을 되풀이하는 용접법을 단속 용접법이라고 한다. 통전시간과 단속시간의 비율은 철강의 경우에 1:1경합금의 경우에는 1:3 정도로 한다. (2) 시임 용접 작업 : 전극의 도전율은 구리의 75% 이상으로 되어야 한다. 전극부에는 발열이 많아 내부를 물로 냉각하든가 또는 외부에서 물로 냉각한다. 시임 용접은 단열의 시임 용접이외도 여러 가지 형식이 있다.또한 판재의 양단부에 전극을 접촉시키면서 전류를 통하여 맞대기 용접과 시임 용접을 동시에 하는 맞대기시임 용점도 있다. 이 방볍은 성형 로울러로 순차적으로 띠판을 원형으로 하고 그 끝을 맞추고 이 부분에양측에서 원판형 전극으로 전류를 통하며 동시에 측면에서 압력을 주어 용접 파이프를 만든다. 저탄소강 및스테인레스강으로 지름 10-127mm , 두께 0.8-6mm 인 판을 용접한다. 전극부는 발열이 심하므로 내부에물을 통과시켜 냉각하며 외부에서 물을 부어 냉각할 때도 있다. |
◆ 프로젝션 용접법 용접하려고 하는 금속판의 한쪽 또는 양쪽에 돌기 부분을 만들어 놓고 압력을 가하면서 전류를 통하면 전류 및 압력이 집중하게 되므로 집중열이 발생하여 용접되게 한 것을 프로젝션 용접이라고 한다. 전극은 평평한 것을 사용하며 스포트 용접과 같은 방법으로 전류를 통하고 용접한다. 그러므로 이것은 스포트 용접의 일종이라고 볼 수 있다. 프로젝션 용접을 하면 돌기부가 가열되어 그 형상이 변화하면서 용접 면적이 증가되므로 과열되는 일이 적다. 열용량이 너무 심하게 변하는 엷은 판과 두꺼운 판을 용접할 때에는 두꺼운 판재를 프로젝션 가공하여 엷은 판과 같이 용접할 수 있다. 프로젝션 가공의 높이는 대체로 판재의 약 1/3 정도로 한다. |
◆ 프로젝션 용접법의 특징 (1) 열용량의 차이가 많은 서로 다른 금속의 접합에서도 좋은 열평형이 얻어진다. (2) 동시에 수개의 용접이 가능하고 작업 속도가 빠르다. (3) 전극의 수명이 길고 작업 능률이 높다. (4) 점 사이의 거리가 작은 스포트 용접이 가능하다. (5) 작은 용접점이 높은 신뢰도 아래에서 쉽게 얻어진다. 이상의 장점이 있으므로 전기 기구 , 자동차 부품 등의 제작에 널리 쓰인다. 또한 프로젝션 용접은 스포트용접의 전극부를 개조하여 그대로 사용할 수도 있으나 일반적으로 동시에 다점 용접용으로 설계되고 전극 가압면적이 넓기 때문에 가압력 및 출력도 그것에 따라 크게 된다. |
◆ 가스 용접 장치 (1) 아세틸렌 가스 아세틸렌 가스는 발생기에서 만들어지고 발생할 때 생긴 불순물을 청정기에서 깨끗이 하고 산소는 산소병에 든 것을 감압 밸브를 통하여 토오치 내부에서 두 가지 가스를 혼합한다. 가스 용접에는 적당한 여러 가지 장치가 필요하다. 그림 6. 산소-아세틸렌 용접 장치의 개략도 아세틸렌은 칼슘카바이드에 물을 작용시키면 쉽게 발생한다. 이때 화학 반응식은 CaC2 + 2H2O --> C2H2 +Ca(OH)2 + 31.872kcal 아세틸렌 외에 수산화칼슘이 발생하여 남게된다. 아세틸렌은 매우 불안정한 탄소와 수소와의 화합물이므로 열을 가하거나 압축하여 압력을 올리든지 하면 곧 분해하여 열을 내며 폭발한다. 그러므로 그늘진 곳에 안전하게 보관하여야 한다. 이것은 아세틸렌에 불순물이 많이 섞여 있기 때문이며 구리 및 황동 등의 기구와 접촉하면 폭발성인 화합물 즉 아세틸라이드가 생기는데 기인되므로 특히 주의하여야 한다. (2) 아세틸렌가스발생장치 이동식과 고정식이 있다. 이동식은 카바이드 용량 10kg 이하의 적은 것이 사용되고 발생량은 최대 6000 l/h 정도로서 저압식으로 사용된다. 고정식 가스 발생기는 다량의 가스가 필요할 때에 사용하며 압력에 의하여 분류하면 된다. (1) 저압식 발생기 (수주 100-250mm) (2) 중압식 발생기 (수주 300-2000mm) (3) 고압식 발생기 (수주 2000-15000mm) 가스 발생장치의 구조에는 투입식 , 주수식 및 침지식 등이 있다 투입식 아세틸렌 발생기는 물속에 카바이드를 투입하는 방법으로 발생된 아세틸렌은 물속에 용해되므로 다소 손실을 보며 슬랙의 제거가 곤란하다. 그러나 물 속을 통과한 청정 작용으로 인하여 아세틸렌의 순도가 좋아진다. 또한 반응열에 의한 온도 상승이 일어나지 않는다. 다량의 가스를 사용하는 공장에서는 이 방식의 발생기가 이용된다. 주수식 아세틸렌 발생기는 카바이드 속에 물을 주입하는 방법으로 온도 상승이 일어나기 쉽고 불순물도 많이 포함되어 있다. 그러나 급수의 자동 조절이 용이하고 슬랙의 제거도 간단하므로 적은 용량의 가스를 사용하는 것에 널리 이용된다. 침지식 아세틸렌 발생기는 투입식과 , 주입식의 중간형에 속한 것으로 소형에 많이 쓰이며 과잉 발생을 일으키기 쉬운 단점이 있다. 그러나 이것은 구조가 간단하고 가스 사용량에 따라 발생량을 자동적으로 조절할 수 있는 장점이 있다. 반응열에 의한 온도 상승이 있는 것은 위험하다. 우리 나라에서 이동식으로 널리 사용하는 것의 대부분은 침지식으로서 이동식을 겸하고 있다. 침지식은 장치가 간단하고 소형이며 가볍고 편리한 가스 발생법이다. 그러나 열의 상승이 많고 또한 가스가 순수하지 못한 단점이 있다. (3) 아세틸렌 청정기 및 안전 장치 가스청정기 : 아세틸렌 발생기에서 발생한 C2H2가스는 인화수소 , 활화수소 , 암모니아 , 일산화탄소 등 해로운 불순물이 혼합되어 용접부에 나쁜 영향을 주기 때문에 이것들을 제거하기 위하여 청정기를 사용한다. 제거에는 수세 여과 화학처리에 의한 아세틸렌 청정법 등이 있으며 보통 화학적 청정법이 사용된다. 구멍이 많이 뚫린 판 위에 청정제를 적당한 높이로 놓고 아래서부터 가스를 통과시켜 청정하는 장치가 쓰인다. 아세틸렌 청정기 및 안전기 : 아세틸렌 발생기에서 발생한 가스 속에는 용접부에 나쁜 영향을 주고 또한 아세틸렌 폭발을 일으키는 불순물이 있기 때문에 이것을 제거하여야 한다. 제거에는 아세틸렌 청정기를 사용한다. 용접 작업 중 역화를 일으키든가 저압식 토오치가 막혀 산소가 아세틸렌 쪽으로 역류하는 경우가 있다. 이 때 역류작용이 발생기까지 미치면 폭발할 위험성이 있으므로 토오치와 발생기의 중간 위치에 안전밸브를 설치하여 이 위험을 방지하고 있다. 일반적으로 수압식 안전 밸브 등이 쓰인다. 용해 아세틸렌 및 아세틸렌 실린더 : 아세틸렌은 아세톤에 잘 용해되는 성질이 있으므로 고압 용기 안에 석면 , 목탄 또는 규조토 등의 다공질 물질을 고르게 넣어 일정한 양의 아세톤을 흡수시키고 15㎏/㎠ 까지 충전시킨 것을 용해 아세틸렌이라 한다. 용해 아세틸렌은 그 취급이 매우 간단하고 아세틸렌과 산소의 혼합비 조절이 용이하고 경제적이므로 널리 쓰인다. 용해 아세틸렌의 장점을 들어보면 (1) 운반이 용이하고 발생기 부속 장치가 필요하지 않다. (2) 고압 토오치를 사용할 수 있다. (3) 순도가 높고 좋은 용접을 할 수 있다. (4) 아세틸렌의 손실이 대단히 적다. (5) 폭발의 위험성이 없다.(4) 아세틸렌 중의 불순물의 영향 가스 절단법에서는 산소의 순도가 중요하지만 용접작업의 경우에는 아세틸렌의 순도가 중요하다. 산소가 불순하면 주로 불꽃 온도에 영향을 주지만 아세틸렌이 불순하면 용착 금속을 해치고 또한 폭발의 위험성까지 가져온다. 황화수소는 강의 용접부를 취성이 생기게 하며 강도를 저하시키고 토오치 , 도관 , 플렌지 , 파이프 등을 부식시킨다. 인화수소는 용접부를 취성을 가지게 하고 다공질로 하며 내식성이 약한 용접부를 만든다. 규화수소는 팁을 소모시키며 또한 팁에 부착하여 역화의 원인이 되며 인화수소도 0.2% 이상 혼입하면 폭발될 위험성이 있다. 암모니아의 존재로 아세틸렌은 구리 , 은 , 수은과 화합하여 폭발성의 화합물을 만든다. 또한 수증기 메탄 수소 질소 등은 불꽃의 온도를 저하시킨다. 위와 같은 불순물 중 황화수소 , 인화수소 , 암모니아 등은 다른 것에 비하여 함유량이 많고 더욱 해롭다. 그러므로 물에 용해하기 쉬운 황화수소 , 암모니아는 충분히 물 속을 통과시켜 함유량을 줄인 후 제거하기 어려운 인화수소를 포함한 가스는 아세틸렌 청정기를 통하여 제거한다. (5) 산소 산소는 공기 또는 물에서 제조되고 있다. 산소 자체는 연소하는 성질을 가지고 있지 않으나 아세틸렌에 혼합하면 아세틸렌과 화합하여 연소하고 고열을 낸다. 산소 실린더 속의 산소는 고압이므로 실린더의 취급에 대해서는 고압가스 단속법 시행 규칙에 따르지 않으면 안 된다. 취급상 주의할 점은 다음과 같다. (a) 운반 중에 충격을 주지 말 것 (b) 연소할 염려가 있는 기름이나 먼지를 피할 것 (c) 직사 광선을 피하여 그늘진 곳에 둘 것 (d) 밸브의 개폐는 조용히 할 것 (e) 산소 누설 시험에는 비눗물을 사용할 것 (6) 압력 조정기 : 용해 아세틸렌 또는 산소 실린더 등의 압력은 대단히 고압이므로 그대로는 사용할 수 없다. 그러므로 토오치의 크기 작업 조건 등에 따라 보통 1-5기압 정도로 감압하여 사용하지 않으면 안 된다. 이와 같이 고압의 가스를 작업에 적합한 압력으로 감압하여 그 조정 압력을 유지하기 위하여 사용되는 기기가 압력 조정기 이다. 도관 : 산소용 고무관은 20㎏/㎤이하 아세틸렌용 고무관은 2㎏/㎤이하에 사용하는 도관을 보통 사용하고 잇다. 산소용은 검은 색 아세틸렌 용은 붉은 색으로 구별하여 혼동하지 않도록 하여야 한다. 도관의 안 지금은 9㎜ , 6㎜ 를 사용하고 길이는 3-5m 를 표준으로 한다. 아세틸렌 가스의 송기 압력의 감소는 10mmHg 를 넘지 않는 것이 적당하다 토오치 : 토오치는 손잡이 , 혼합실 , 팁의 세 부분으로 되어 있고 손잡이에는 산소 및 아세틸렌용 고무관을 연결하는 연결관이 있다. 저압식 토오치는 아세틸렌 가스의 압력이 0.07㎏/㎤ 기압 이하일 때 쓰이며 인젝터 형으로 되어 있고 분출하는 산소 기류로 아세틸렌을 끌어 내어 혼합한다. 중압식 토오치는 0.07-1.3㎏/㎤ 기압 그리고 고압식은 1.5㎏/㎤ 이상에서 쓰이는 것으로 인젝터형도 있으나 등압가스 혼합식이 사용되어 좋은 결과를 나타내고 있다. (7) 팁 : 토오치의 선단에는 팁이 있다 이것은 일반적으로 번호로 표시하고 독일식 팁의 번호는 연강판의 용접 가능판 두께를 표시하는데 가령 10번은 10㎜의 연강판이 용접 가능한 것을 표시하고 있다. 프랑스식 용접기는 산소 분출구에 니들 벨브를 가지고 있으며 산소 분출구의 크기를 팁에 맞추어서 어느 정도 조절할 수 있게 되어있다.. 더구나 산소 분출구가 토오치에 설치되어 있으므로 팁이 소형 경량으로 되어야 작업하기가 쉽다. (8) 가스의 연소 , 용접봉 , 용제 산소와 아세틸렌을 거의 같은 용적으로 혼합하여 팁에서 분출시켜 가스를 연소시키면 불꽃은 속불꽃과 겉불꽃으로 나뉘어 진다. |
'기술자료' 카테고리의 다른 글
4.텅스텐 아크용접 (0) | 2022.11.22 |
---|---|
3.피복 아크용접 (0) | 2022.11.22 |
용접의 개념 (1) | 2022.11.22 |
[스크랩] 강의열처리기초이론 (1) | 2022.11.16 |
[스크랩] 금속 열처리 종류 및 방법 (2) | 2022.11.16 |